Manufacturing sites are bustling environments where machinery, equipment, and a busy workforce operate together to produce goods. The very nature of this industrial activity can lead to degraded flooring due to wear and tear. As a result, restoring flooring is a critical task that can significantly impact a site’s safety, productivity, and aesthetics. This guide outlines the key steps necessary for flooring restoration in manufacturing environments, helping operators maintain their facilities efficiently and effectively.
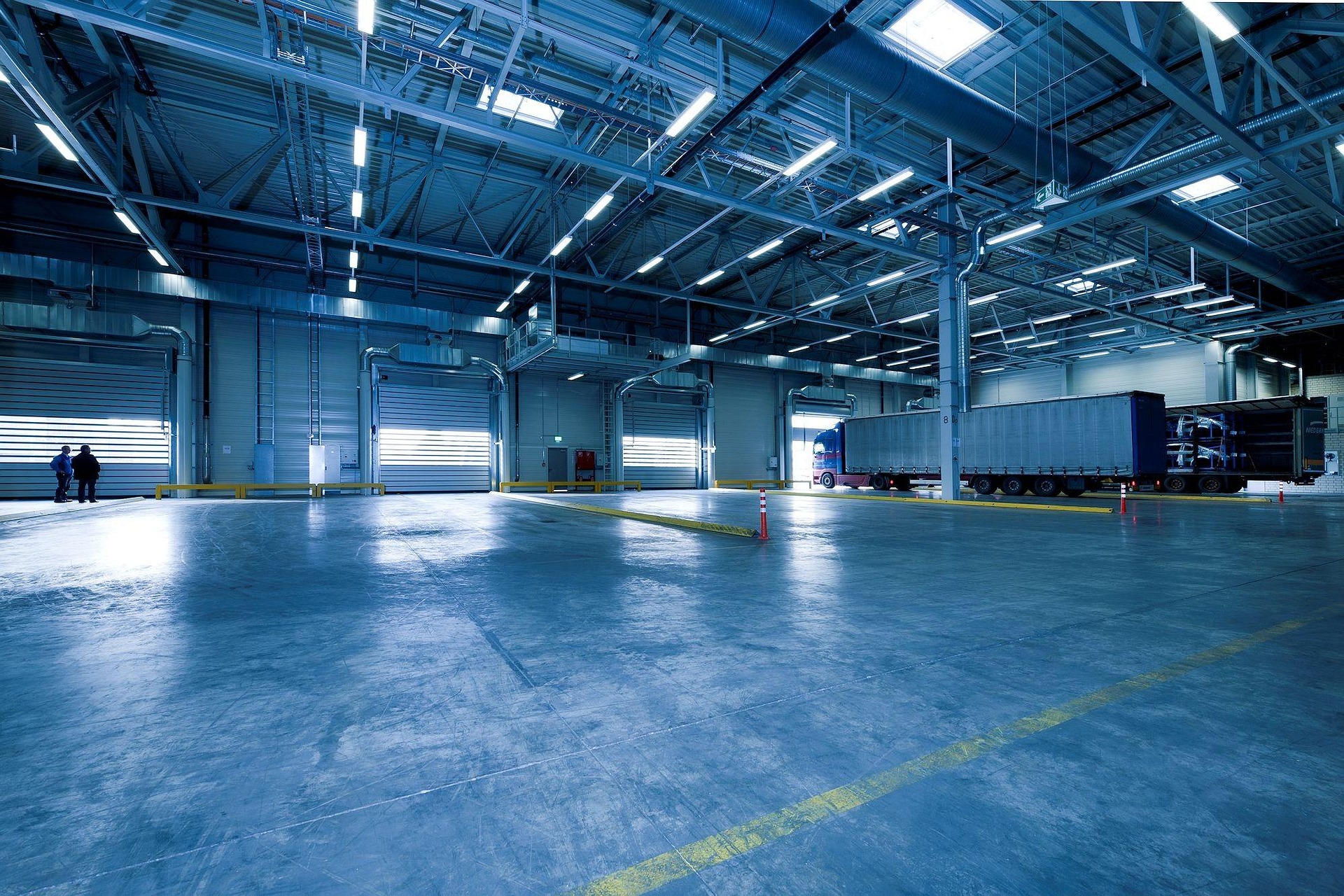
Assessing the Condition of Your Floor
The first step in any flooring restoration project is to assess the current condition of your floor. This assessment involves a thorough inspection to identify cracks, stains, and other signs of damage that could affect performance. It’s good to pay close attention to areas that experience high foot traffic and heavy machinery use. According to a study by The Concrete Society, over 80% of industrial flooring failures can be traced back to poor surface preparation and insufficient initial assessments.
Typically, operators should look for specific indicators such as surface wear, unevenness, moisture ingress, and any chemical damage. Creating a detailed report of findings during this assessment helps to set the stage for necessary repairs and can serve as a reference point for future maintenance. By understanding the condition of the flooring, management can make informed decisions that prioritize safety and operational efficiency.
Defining the Restoration Goals
Once you have assessed the condition of the flooring, the next step is to clearly define your restoration goals. Are you aiming to improve safety by repairing dangerous cracks? Or perhaps your objective is to enhance the aesthetic of your facility to create a more appealing working environment. Understanding your goals will influence the choice of materials and restoration methods to be used. This process may involve consulting with manufacturers or contractors who specialize in concrete repair or flooring systems.
By ensuring that all stakeholders are involved in defining these goals, management can foster a clearer vision of the end result, streamlining the restoration process. Identifying whether you want a temporary fix or a long-lasting solution will help in selecting the appropriate materials and techniques tailored to your specific needs.
Preparing the Area for Restoration
Preparation is key to successful flooring restoration. This phase involves cleaning the area thoroughly to remove debris, dust, and any contaminants that could interfere with bonding agents or curing processes. Specific preparation might include repairing underlying structural issues. According to the National Association of Home Builders, an estimated $10 billion is spent annually on flooring renovations due to improper preparation practices.
During this phase, consider utilizing appropriate safety equipment and protective gear. It’s advisable to mark out the area to ensure that the restoration crew can work without interruptions. If heavy machinery is involved in working around the area, securing the site to prevent accidents becomes a priority. This increases safety and often decreases downtime, reinforcing operational productivity.
Selecting the Right Materials
After preparation, the selection of suitable restoration materials is paramount. Factors such as the type of flooring, chemical exposure, and environmental conditions must be taken into account. Epoxy coatings are popular for their durability and resistance to commercial cleaning agents. According to the American Society for Testing and Materials, 95% of industrial facilities reported greater floor longevity after switching to epoxy systems. For environments requiring enhanced visibility and lighting, consider implementing industrial lights as part of your restoration efforts. This addition boosts safety and allows workers to maintain a keen eye on the workspace, preventing accidents due to insufficient lighting. Selecting the right materials can determine the success and longevity of the restoration initiative.
Implementing the Restoration Process
Now that all preparatory work and planning is complete, it’s time to implement the restoration process. This phase may involve various tasks, from applying coatings and curing with HID lights to grinding the surface for a smoother finish. The techniques employed will depend on the materials previously selected and the specific objectives set out at the beginning. Engaging skilled labor teams or professionals who specialize in flooring restoration can dramatically improve both the quality of work and the outcome.
It’s crucial during this phase to monitor environmental conditions to ensure that curing times are adhered to and that the materials are being applied under optimal conditions. Missteps during this phase can lead to long-term issues, such as peeling or other failures in the flooring system.
Post-Restoration Maintenance
After completing the restoration process, maintaining the new flooring is vital to ensure longevity. The maintenance strategy should be based on the materials used, addressing elements such as cleaning frequencies and protection against chemical spills. Scheduling regular inspections and maintenance routines can extend the useful life of the flooring while ensuring that potential issues are detected early. The flooring should be monitored closely, specifically within the first months of use, as this period is critical to assess the efficacy of the restoration work.
Consider implementing training for staff on the appropriate ways to maintain the floor. This promotes a culture of care among employees and encourages them to understand the importance of preserving the working environment.
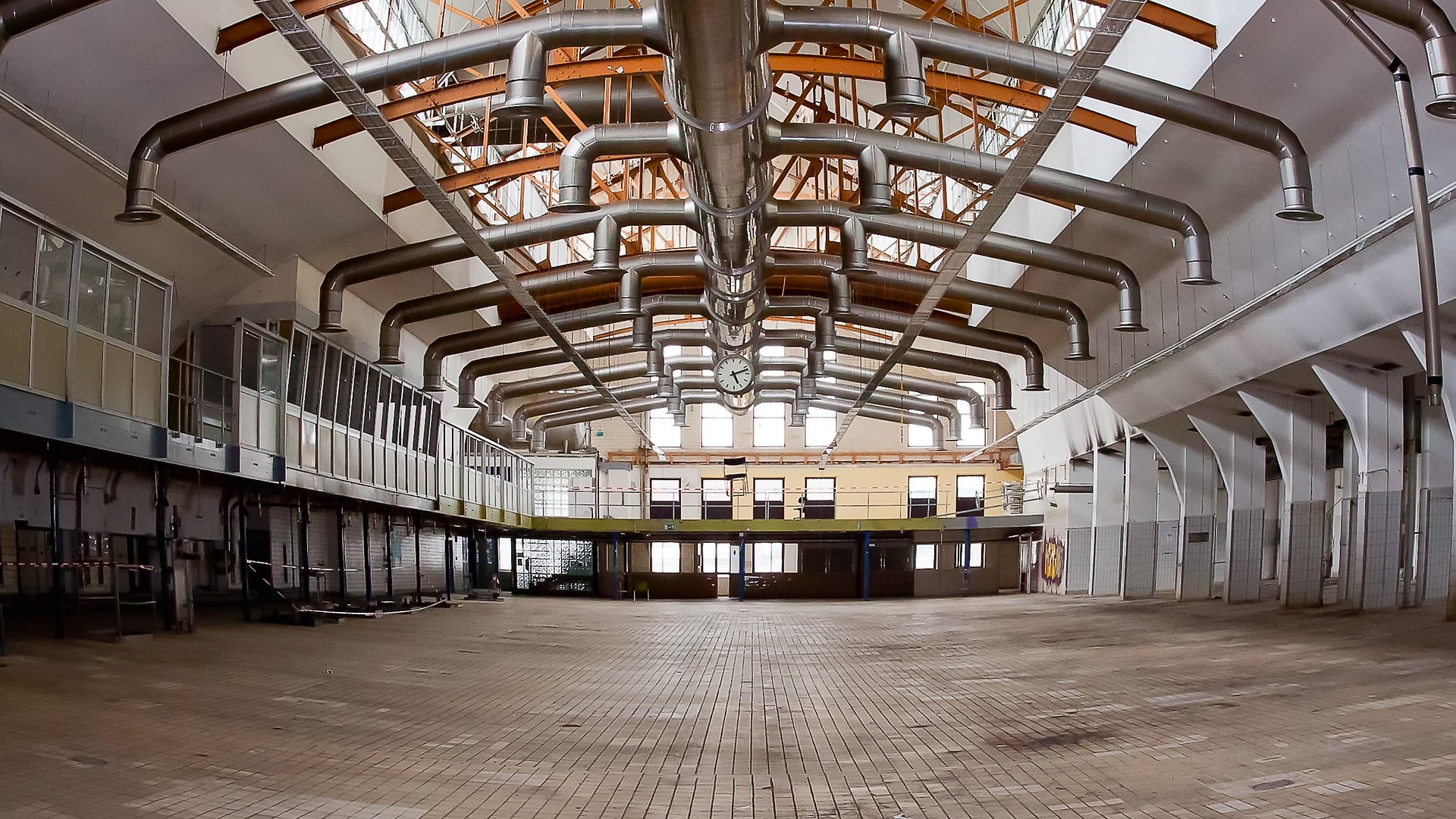
Maintaining an appealing aesthetic can positively influence client perceptions, setting a strong image of professionalism and care in business. This commitment to facility upkeep can promote enhanced workplace satisfaction among staff, contributing to higher retention rates and a more harmonious work environment.

HedgeThink.com is the fund industry’s leading news, research and analysis source for individual and institutional accredited investors and professionals